The Ohio train wreck
On Feb 03, 2023 freight train 32N, operated by Norfolk Southern and carrying a mix of hazardous and non hazardous material, derailed near East Palestine Ohio.
This led to a fire and damage to the rail cars that contained Vinyl Chloride. To avoid an uncontrolled explosion of Vinyl Chloride, the authorities decided to release it and trigger a controlled explosion and burn. This led to a huge chemical cloud over the area.
Ohio Train derailment Root Cause
We had correctly speculated on this blog here that the root cause of the Ohio train derailment seemed to be an overheated bearing. This Ohio train derailment cause has now been confirmed by the NTSB report here.
The hazardous material in the derailed rail cars, included Vinyl Chloride, a highly toxic material that decomposes violently when exposed to air or water and releases noxious gases such as Hydrogen Chloride and Phosgene (which is extemely toxic to all living beings and was actually used as chemical weapon in World War I).
According to the NTSB report, Train 32N comprised 2 head-end locomotives, 149 railcars, and 1 distributed power locomotive located between railcars 109 and 110. They included 20
placarded hazardous materials tank cars, transporting combustible liquids, flammable
liquids, and flammable gas, including vinyl chloride.
Train 32N was operating with a dynamic brake application as the train passed a
wayside defect detector on the east side of Palestine, Ohio, at milepost (MP) 49.81.4
The wayside defect detector, or hot bearing detector (HBD), transmitted a critical audible alarm message instructing the crew to slow and stop the train to inspect a hot axle. The train engineer increased the dynamic brake application to further slow and stop the train. During this deceleration, an automatic emergency brake application initiated, and train 32N came to a stop.
Hot Box Detector
What exactly is a Hot Box Detector (HBD for short)?
According to Wikipedia ( https://en.wikipedia.org/wiki/Hot_box)
A hot box is the term used when an axle bearing overheats on a piece of railway rolling stock. The term is derived from the journal-bearing trucks used before the mid-20th century. The axle bearings were housed in a box that used oil-soaked rags or cotton (collectively called “packing”) to reduce the friction of the axle against the truck frame. When the oil leaked or dried out, the bearings overheated, often starting a fire that could destroy the entire railroad car (and cars coupled to it) if not detected early enough.
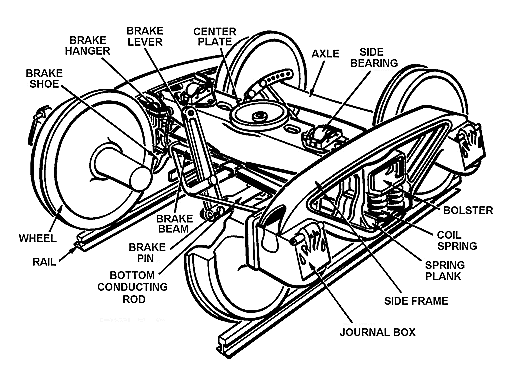
Pic Credit: https://commons.wikimedia.org/
The packing and bearing had to be regularly inspected by yard crews, and packing was often added at major stops. The journal bearing was replaceable, but if neglected, it would heat to a temperature where the babbitt bearing alloy would melt away, leaving the brass carrier riding on the steel axle, and result in a “taper journal”. This would eventually lead to the axle fracturing and the car above falling onto the wheel, or failure of the taper journal, causing the side frame and journal box to fall below the level of the rails, either of which could cause a major derailment of the train.
So this is a well known cause of train derailments, fires and other incidents for many decades. It is not something that is newly discovered.
High Temperature Alarms ignored?
Before the emergency stop and derailment, Train 32N passed three HBD systems on its trip before the derailment.
At MP 79.9, the suspect bearing from the 23rd car had a recorded temperature of 38°F above ambient temperature.The train crew should have taken some sort of an action at this point of time, if one assumes that the HBD alarm did reach them.
When train 32N passed the next HBD, at MP 69.01, the bearing’s recorded temperature was 103°F above ambient. After two such alarms, the train crew should have definitely stopped the train and corrected the situation. This of course assumes that they were alerted (the alarm did sound in the locomotive cabin or caboose).
The third HBD, at MP 49.81, recorded the suspect bearing’s temperature at 253°F above ambient. NS has established the following HBD alarm thresholds (above ambient temperature) and criteria for bearings:
• Between 170°F and 200°F, warm bearing (non-critical); stop and inspect
• A difference between bearings on the same axle greater than or equal
to 115°F (non-critical); stop and inspect
• Greater than 200°F (critical); set out railcar.
Although the NTSB report does not say this specifically, but if the earlier alarms had been acted upon, probably the bearing and axle would not have overheated to the point where they caught fire.
That they did catch fire was observed on CCTV surveillance footage from a camera mounted on the perimeter of a large industrial plant near the tracks, before the train derailed.
Conclusion
Although this is a preliminary report, it does appear that the root cause of the accident was overheated or defective bearings. Maintenance does play an important role in preventing accidents. Secondly, the staff should be trained to take action on maintenance alarms to prevent such incident. This of course assumes that the HBD alarm signals did reach the train crew.
Periodic proof testing of such systems is essential to know about failures as soon as it happens and prevent accidents.